A Comprehensive Guide to the Refine and Benefits of Plastic Extrusion
In the large world of production, plastic extrusion emerges as a highly efficient and necessary procedure. Transmuting raw plastic right into continuous profiles, it caters to a wide variety of markets with its impressive flexibility.
Comprehending the Essentials of Plastic Extrusion
While it might show up facility at first glance, the process of plastic extrusion is essentially simple - plastic extrusion. It is a high-volume manufacturing technique in which raw plastic is melted and shaped into a continuous profile. The process starts with the feeding of plastic product, in the kind of granules, pellets, or powders, right into a warmed barrel. The plastic is then melted using a combination of heat and shear, used by a revolving screw. As soon as the molten plastic gets to completion of the barrel, it is required through a small opening referred to as a die, shaping it into a desired kind. The designed plastic is then cooled, solidified, and reduced right into preferred lengths, completing the procedure.
The Technical Process of Plastic Extrusion Explained

Sorts Of Plastic Suitable for Extrusion
The selection of the appropriate type of plastic is a vital aspect of the extrusion procedure. Various plastics supply special properties, making them a lot more suited to particular applications. Comprehending these plastic kinds can considerably boost the extrusion process.
Contrasting Plastic Extrusion to Other Plastic Forming Approaches
Understanding the kinds of plastic suitable for extrusion leads the way for a more comprehensive discussion on just how plastic extrusion stacks up against various other plastic forming approaches. These include injection molding, impact molding, and thermoforming. Each technique has its one-of-a-kind uses and benefits. Injection molding, for circumstances, is outstanding for developing elaborate components, while blow molding is best for hollow things like bottles. Thermoforming excels at creating shallow or large parts. Plastic extrusion is exceptional when it comes to developing continual accounts, such as seals, gaskets, and pipes. It additionally enables a consistent cross-section along the length of the product. Thus, the option of technique greatly depends on the end-product demands and specs.
Secret Advantages of Plastic Extrusion in Manufacturing
In the world of production, plastic extrusion provides several significant benefits. One notable benefit is the cost-effectiveness of the procedure, that makes it a financially attractive production method. Additionally, this strategy gives exceptional product versatility and boosted manufacturing speed, thereby increasing total production effectiveness.
Economical Production Method
Plastic extrusion leaps to the forefront as an economical manufacturing technique in production. In addition, plastic extrusion calls for much less power than typical production approaches, adding to reduced functional prices. On the whole, the economic advantages make plastic extrusion an extremely appealing alternative in the production sector.
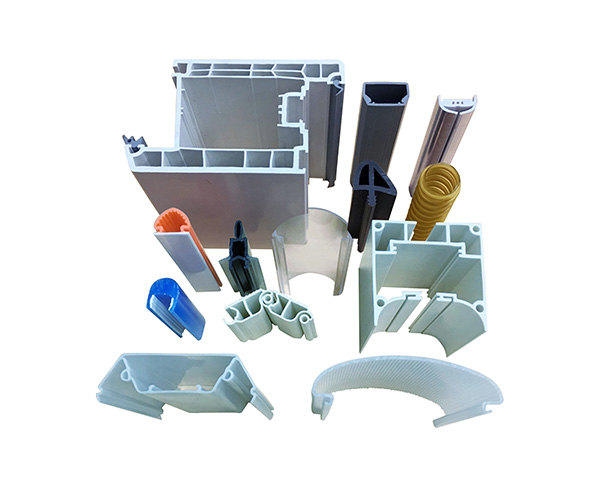
Superior Product Versatility
Beyond the wikipedia reference cost-effectiveness of click resources plastic extrusion, an additional significant advantage in making lies in its remarkable product adaptability. This makes plastic extrusion an excellent service for markets that need customized plastic elements, such as vehicle, building, and packaging. In essence, plastic extrusion's item versatility fosters innovation while improving operational performance.
Enhanced Manufacturing Rate
A considerable benefit of plastic extrusion lies in its enhanced production rate. Couple of other manufacturing procedures can match the rate of plastic extrusion. Furthermore, the ability to anchor maintain regular high-speed production without sacrificing item quality establishes plastic extrusion apart from other techniques.
Real-world Applications and Effects of Plastic Extrusion
In the world of production, the technique of plastic extrusion holds extensive importance. The economic advantage of plastic extrusion, mainly its cost-efficient and high-volume result, has actually transformed manufacturing. The industry is persistently striving for innovations in recyclable and naturally degradable materials, indicating a future where the benefits of plastic extrusion can be retained without compromising ecological sustainability.
Verdict
In conclusion, plastic extrusion is a highly reliable and reliable technique of transforming raw materials right into varied products. It provides numerous benefits over various other plastic developing methods, including cost-effectiveness, high output, minimal waste, and design adaptability. Its influence is exceptionally felt in numerous markets such as construction, automotive, and durable goods, making it a pivotal procedure in today's production landscape.
Digging deeper right into the technical procedure of plastic extrusion, it begins with the selection of the ideal plastic material. Once cooled down, the plastic is cut right into the needed lengths or injury onto reels if the product is a plastic movie or sheet - plastic extrusion. Comparing Plastic Extrusion to Various Other Plastic Forming Techniques
Understanding the kinds of plastic suitable for extrusion leads the way for a more comprehensive discussion on just how plastic extrusion stacks up versus other plastic developing methods. Couple of various other manufacturing procedures can match the speed of plastic extrusion.
Comments on “Plastic extrusion for efficient, scalable manufacturing solutions”